Understanding the Importance of Pressure Die Casting Manufacturers
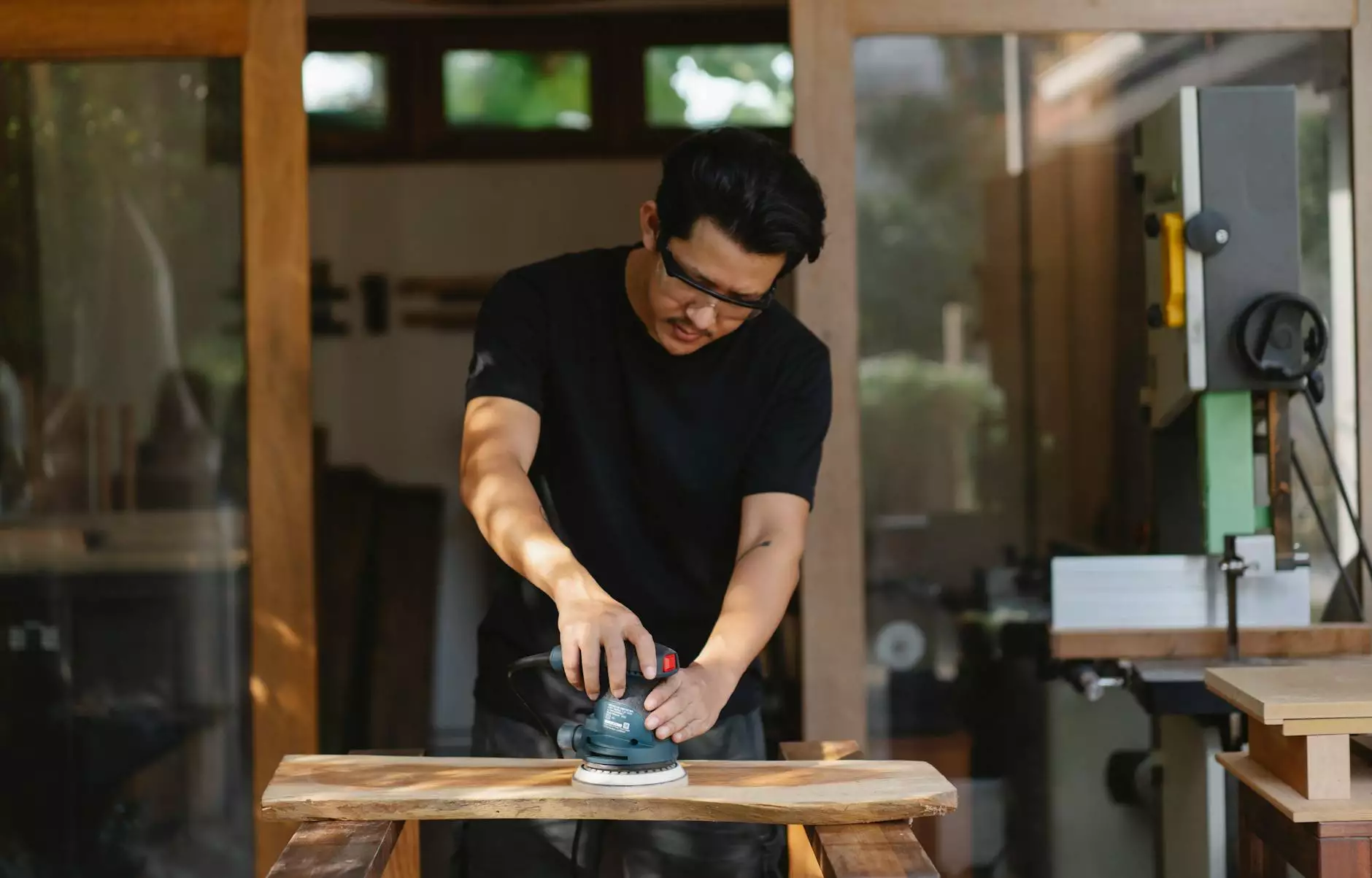
In the realm of modern manufacturing, the role of pressure die casting manufacturers cannot be understated. This method of production has revolutionized the way parts and components are made, particularly in industries that demand precision and efficiency. In this extensive article, we will explore what pressure die casting is, the benefits it offers, the manufacturing process, and how manufacturers like Deep Mould stand out in this competitive field.
What is Pressure Die Casting?
Pressure die casting is a sophisticated manufacturing process that involves the injection of molten metal into a steel mold under high pressure. This technique is widely used for producing components that require precise dimensions and specifications. The materials commonly utilized in this process include aluminum, zinc, and magnesium, making it a versatile option for manufacturers seeking high-quality metal parts.
The Benefits of Pressure Die Casting
There are several advantages associated with using pressure die casting manufacturers. Let’s delve deeper into these benefits:
- High Precision: One of the primary advantages of pressure die casting is the ability to produce components with extremely tight tolerances. This precision is essential in industries such as automotive and aerospace, where safety and performance are paramount.
- Cost-Effective Production: Mass production becomes more economically viable with pressure die casting. The production speed and the minimal waste generated in this process contribute to lower overall costs.
- Complex Shapes: This method allows for the creation of complex geometries that would be nearly impossible with other manufacturing techniques. This flexibility is invaluable for design engineers seeking innovative solutions.
- Superior Surface Finish: Parts produced through pressure die casting often require little to no additional finishing, thanks to the smooth nature of the mold, resulting in reduced post-processing times.
- Material Efficiency: The process uses less material compared to other methods. As the molten metal is injected directly into the mold, there is minimal scrap generation, leading to both environmental and economic benefits.
The Process of Pressure Die Casting
The workflow of pressure die casting can be broken down into several key steps:
- Dies Preparation: The process begins with manufacturing the die, which is typically made from high-quality steel. The die must be designed to withstand high pressure and repeated use.
- Melting the Metal: The chosen metal, usually aluminum or zinc, is melted in a furnace. This step requires precise temperature control to ensure the metal is ready for injection.
- Injection: The molten metal is injected into the prepared die at high pressure. This pressure forces the metal into all areas of the mold, ensuring complete filling.
- Cooling: Once the mold is filled, the metal is allowed to cool and solidify. The cooling time can vary depending on the size and complexity of the part.
- Die Opening: After the part has cooled sufficiently, the die is opened, and the finished part is ejected. This must be done carefully to avoid damaging the part.
- Trimming and Finishing: Any excess metal is removed, and further finishing processes may be applied if necessary. This ensures that the part meets the required specifications.
Applications of Pressure Die Casting
Pressure die casting is utilized across a diverse range of industries. Some of the most common applications include:
- Automotive Industry: Components such as engine blocks, transmission housings, and wheel rims are frequently produced using pressure die casting.
- Aerospace Industry: Critical parts that require high strength-to-weight ratios are often manufactured through this process, ensuring optimal performance and safety.
- Consumer Electronics: Many electronic devices, from smartphones to laptops, utilize parts made through pressure die casting for their housings and structural components.
- Industrial Machinery: Pressure die casting is employed in making various machinery components that require durability and reliability.
Choosing the Right Pressure Die Casting Manufacturer
When selecting a pressure die casting manufacturer, it’s essential to consider several factors to ensure high-quality output and efficient production:
1. Expertise and Experience
Choose a manufacturer with extensive experience in pressure die casting. Established companies, like Deep Mould, have a proven track record of delivering quality parts and can provide expert guidance throughout the project.
2. Quality Assurance Procedures
Ensure that the manufacturer employs rigorous quality control measures. This includes regular inspections and testing of the parts produced to confirm they meet industry standards.
3. Advanced Technology
The use of the latest technologies in the manufacturing process can significantly affect the quality and efficiency of production. Look for manufacturers who invest in modern casting equipment.
4. Customization Capabilities
Your manufacturing needs may vary, and having a manufacturer that can customize their processes to meet your specific requirements is crucial.
5. Delivery Timeliness
Discuss lead times and delivery schedules upfront to ensure that the manufacturer can meet your project's timelines. Reliability in this aspect is paramount.
Future Trends in Pressure Die Casting
The landscape of pressure die casting is rapidly evolving. As industries focus more on sustainability, manufacturers are starting to embrace eco-friendly practices. Some promising trends include:
- Recyclable Materials: There is a growing interest in using recyclable metals and creating processes that reduce waste.
- Automation and Robotics: The incorporation of automated systems and robotic arms in the manufacturing process is expected to increase efficiency and reduce labor costs.
- 3D Printing of Molds: The use of 3D printing technology to create molds is gaining traction. This innovation allows for faster prototyping and the creation of more complex designs.
Conclusion
Pressure die casting manufacturers play a vital role in the manufacturing sector, delivering high-quality components across various industries. By understanding the advantages of this process, the key steps involved, and how to choose the right manufacturer, businesses can significantly enhance their production capabilities. Companies like Deep Mould exemplify the standards of excellence in this field, ensuring that their clients receive unmatched quality and service.
As we look to the future, embracing innovative trends and technologies will be essential for manufacturers to remain competitive and efficient in an ever-evolving market.