Your Leading **Die Casting Supplier**: Elevating Manufacturing Standards
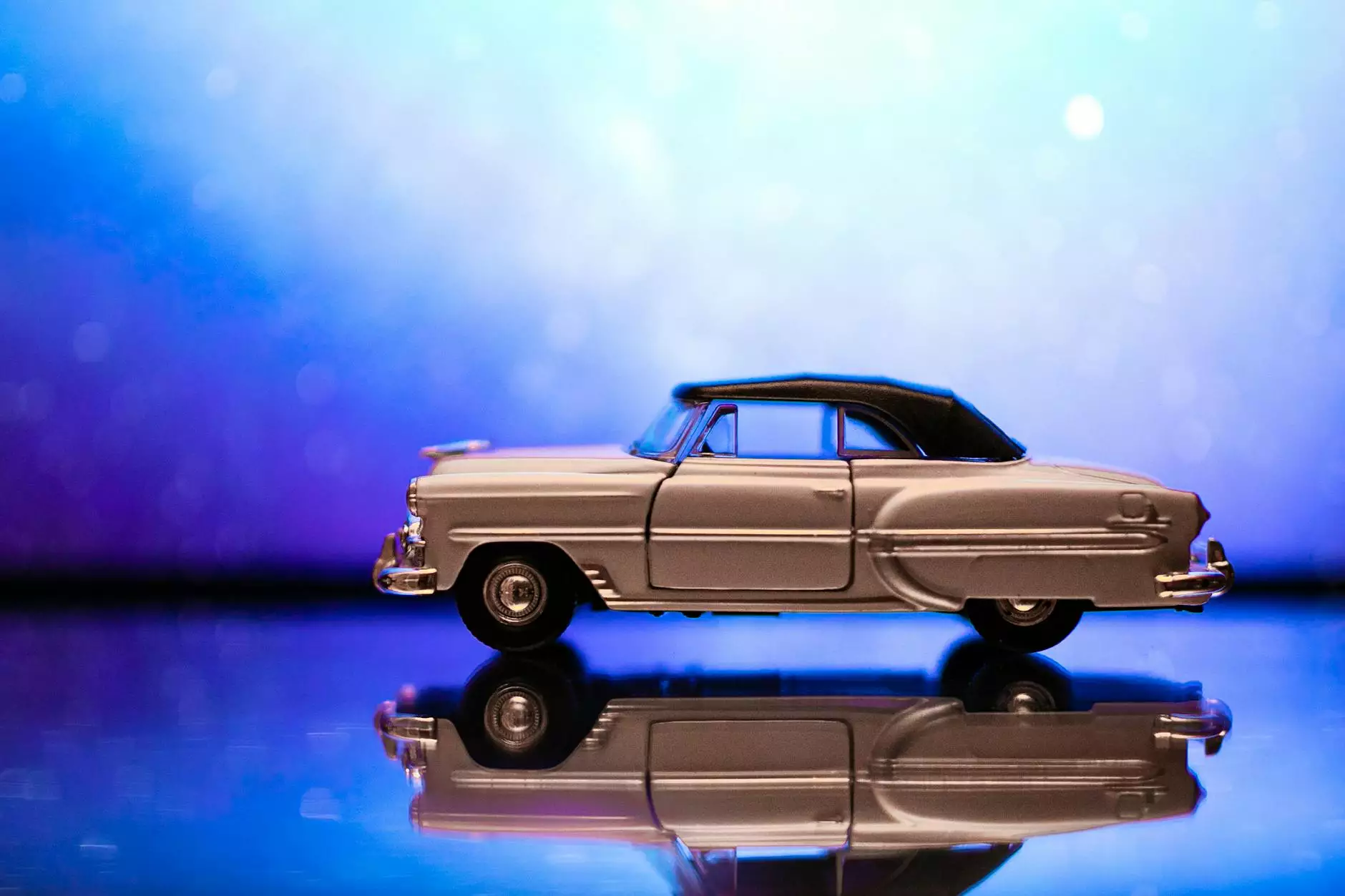
In today’s manufacturing landscape, the choice of materials and production methods can significantly affect the quality and cost of final products. As businesses strive for efficiency and quality, die casting has emerged as a crucial process, particularly with the aid of a reliable die casting supplier. This article will delve into the intricacies of the die casting process, its benefits, the essential qualities to look for in a die casting supplier, and a comprehensive overview of our services at Deep Mould.
Understanding Die Casting: A Brief Overview
Die casting is a metal casting process that involves forcing molten metal into a mold cavity under high pressure. The process can accommodate a variety of metals, including aluminum, zinc, magnesium, and copper. Die casting is favored for its ability to produce intricate shapes that require minimal secondary processing, offering a perfect blend of efficiency and precision.
The Process of Die Casting
The die casting process can be broken down into several key steps:
- Mold Creation: Initially, a die (the mold) is created which comprises two halves. These dies are manufactured from sturdy materials to withstand high pressure.
- Metal Melting: The chosen metal is melted in a furnace to achieve the desired liquid state.
- Injection: Once the metal is molten, it is injected into the die at high pressure, allowing for an accurate, fast fill.
- Cooling and Solidification: After the mold is filled, the metal cools and solidifies, taking on the shape of the mold.
- Mold Opening and Part Removal: Finally, the die halves are separated, and the finished part is removed.
The Advantages of Die Casting
Choosing die casting as a manufacturing process offers numerous advantages:
- High Precision: Die casting provides greater dimensional accuracy and product consistency.
- Complex Geometries: The technique allows for the production of complex shapes that are often difficult to achieve with other methods.
- Cost Efficacy: Over time, die casting reduces manufacturing costs due to its efficiency and speed.
- Surface Finish: Parts produced often require minimal finishing work, resulting in lower costs.
- Material Versatility: Various metal types can be used, each with its own unique properties, enabling specialized applications.
Choosing the Right Die Casting Supplier
The choice of die casting supplier is crucial for businesses seeking superior quality parts. Here are some essential factors to consider:
Experience and Expertise
Opting for an experienced supplier can make a difference in the quality of outputs. Look for a provider with a proven track record in the industry and expertise in various metal fabrication processes.
Quality Assurance Practices
High-quality standards are non-negotiable. Ensure that your supplier adheres to recognized quality assurance protocols and possesses relevant certifications. At Deep Mould, we pride ourselves on our rigorous quality control processes, ensuring that every part we produce meets the highest industry standards.
Advanced Technology and Equipment
A reliable die casting supplier should utilize state-of-the-art technology, which allows for greater precision and efficiency. Evaluate the machinery and tools available and their capabilities in producing complex die cast parts.
Customizability and Flexibility
Each project is unique, and a good supplier should offer custom solutions tailored to your specific needs. From design assistance to material selection and production methods, flexibility is key.
Customer Support
Strong customer support adds significant value to your partnership. Look for a supplier committed to communication and transparency throughout the manufacturing process.
Deep Mould: Your Trusted Die Casting Supplier
At Deep Mould, we aim to be your die casting supplier of choice, providing unmatched quality and service. Our dedication to excellence is reflected in every phase of the manufacturing process:
Innovative Design Solutions
Our team collaborates with clients to develop innovative designs that maximize the advantages of die casting. This includes thorough analysis and prototyping to ensure optimal results in the final product.
State-of-the-Art Facilities
Equipped with cutting-edge technology and modern machinery, Deep Mould is well-positioned to handle projects of any size and complexity. Our facilities undergo regular upgrades to incorporate the latest advancements in die casting technology.
Comprehensive Service Offerings
We offer a wide range of services, from initial design consultation to the final production of die cast parts. Our competencies ensure that we can accommodate various industries, including automotive, aerospace, electronics, and more.
Industries Served by Deep Mould
As a premier die casting supplier, we cater to a broad spectrum of industries, providing tailored solutions that meet their specific needs:
- Automotive: High-quality components for vehicles that meet stringent safety and performance standards.
- Aerospace: Precision-engineered parts that comply with the rigorous regulations of the aerospace sector.
- Electronics: Custom parts for various electronic devices, featuring superior conductivity and durability.
- Consumer Goods: Attractive and functional die cast components for household products.
The Future of Die Casting
The die casting industry is evolving, driven by advancements in technology, materials, and sustainability practices. As the world shifts towards greener manufacturing techniques, die casting suppliers like Deep Mould are adapting to meet these growing expectations. Our commitment to sustainable practices includes:
- Energy Efficiency: We continuously seek ways to reduce energy consumption in our production processes.
- Recyclable Materials: Utilizing recyclable metals helps minimize waste and supports environmental conservation.
- Process Optimization: Implementing lean manufacturing techniques to reduce waste and improve efficiency.
Summary
In summary, choosing the right die casting supplier is vital for ensuring high-quality, cost-effective solutions in the manufacturing realm. As a leading supplier, Deep Mould prides itself on its exceptional quality, innovative solutions, and commitment to customer satisfaction. With our state-of-the-art facilities, expert team, and diverse service offerings, we are poised to meet your die casting needs now and into the future.
For inquiries or to discuss your next project, do not hesitate to contact us. Let Deep Mould be your partner in driving innovation and quality in your manufacturing processes.